Michael Naylor • January 26, 2020
Automate Your Hand or Manual Filling Systems
Boost the productivity of your processes and people
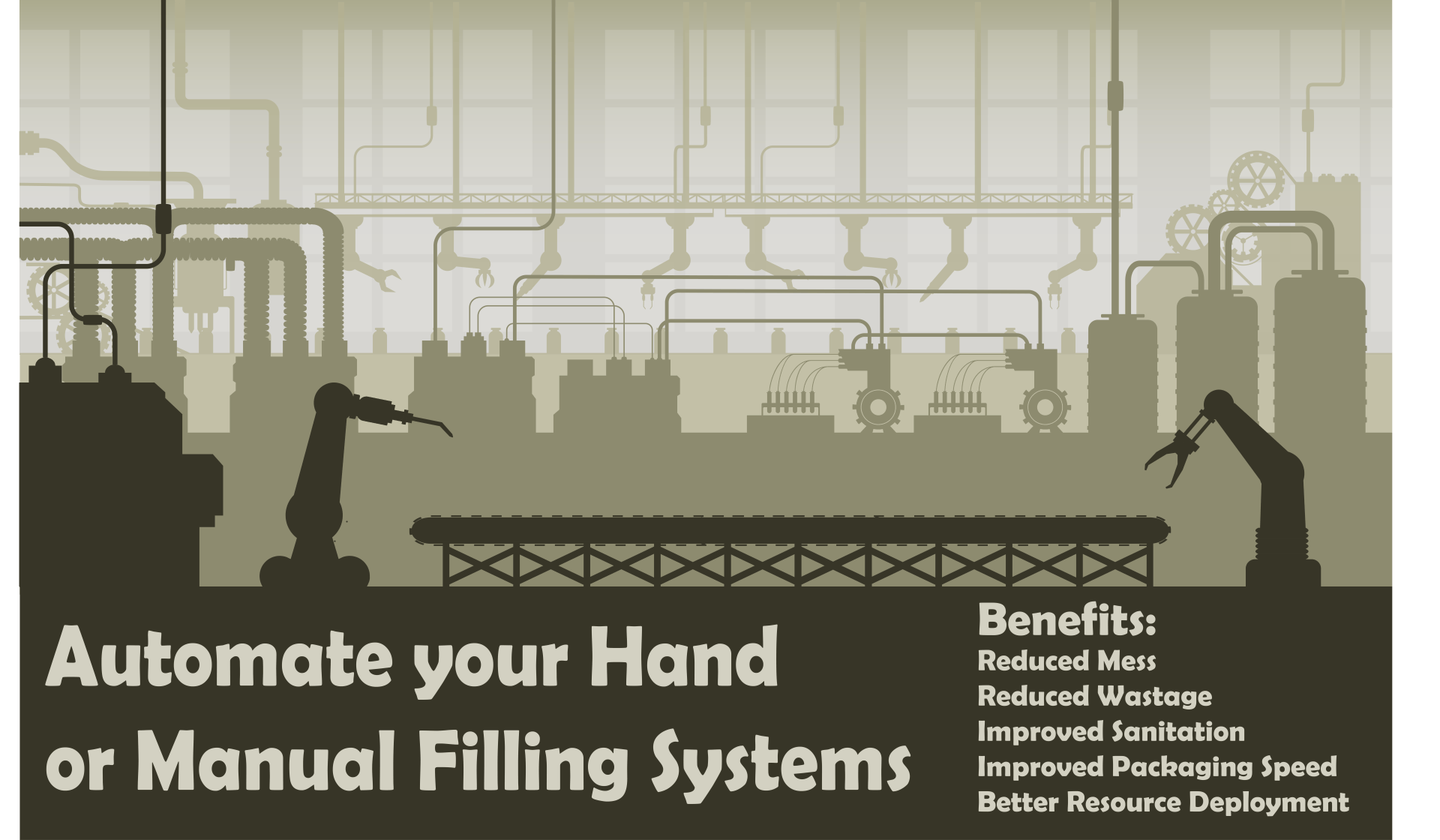
Food processing companies the world over, go through high levels of scrutiny by their respective governing bodies. In addition to regulatory compliance, you also have to strike a delicate balance between consumer demands, and business productivity and profitability. It’s not surprising then, that you are always exploring options to make each step in the production process simpler, faster, cheaper, and safer.
One such critical step is the food filling systems within your setup. If your packaging processes are still dependent on hand filling or manual filling, it is time to consider automating your food filling requirements.
Moving to Automated Food Filling Systems Has Many Advantages
Depending on the type of food you fill and the containers you use, your food filling processes could range from easy to complex.
1. Food Type: Do you package wet foods, such as cooked rice, refrigerated salad, cut fruits, cut vegetables, or shredded meat? Does your operation involve more dry food items, such as cereal, trail mixes, pet food, and such? Whether it is dry or wet, all these food items can be tricky to fill, due to their texture, temperature, and consistency.
2. Container Type: While a plate, cup, or carton may be relatively simple to fill, a jar or pouch typically offers a limited opening, and tray packaging may demand filling of multiple products into the defined compartments.
With manual food filling, your workers will be scooping up these foods with spoons, their hands, or other manual equipment to fill each container. Which means, you will face issues of spillage, wastage and inaccurate weights. Moving to automated food filling systems, such as a volumetric filling machine could positively influence your business productivity at multiple levels:
• Reduced Mess and Wastage: It is not tough to imagine the difference between manually scooping and filling a product versus letting a machine do that job. No spills equals to no mess and no wastage. Essentially, you will be packing and selling that additional product which otherwise ends up on your production floor or filling station.
• Improved Sanitation and Accuracy: While your customers may not complain about overfilling, your leadership team most likely will! Similarly, underfilling or hygiene issues during filling are undesirable. Machine filling will ensure accurate, consistent quantities, precise volumes, and better sanitation. Essentially, automation will help you remain compliant with the applicable laws and stay in the good books of consumer protection bodies.
• Improved Packaging Speed: Every business that tracks production efficiencies already knows how they can make it better. For example, let’s say your data shows that filling 5 additional containers per minute could improve your production time by 20%. While such statistics are good to know, they may be tough to implement in a manual filling process. However, selecting and installing the right filling machine could help make the necessary improvements in your production speed and efficiency.
• Better Resource Deployment: Imagine how many other processes you could reinforce, by redeploying your workers into tasks that need manual intervention. This could improve your resource utilization and productivity, in turn boosting your business productivity. Moreover, your workers will get an opportunity to learn a new skill, and contribute to a different process within the production line.
Enhance Business Productivity with Multi-Fill’s Volumetric Filling Solutions
At Multi-Fill, we offer a variety of unique volumetric fillers
and high speed counting machines
to help you automate your food filling processes. Our designs are compact, versatile, and customizable to the rest of your production setup, making your automation project simple, efficient and affordable.
Scale up your business productivity through world class solutions from Multi-Fill. Call us at 801-280-1570 to explore our full suite of products, or contact us online.
Designing a food filling line: Product is king

Food packaging plays a vital role in ensuring the safety and quality of the food we consume. To maintain high standards and prevent foodborne illnesses, the food packaging industry follows a set of regulations known as Current Good Manufacturing Practices (cGMP). In this article, we will delve into cGMP and explore its impact on preventing foodborne illness. We will also take an inside look at how cGMP is implemented on a food factory line, the role of food filling equipment in ensuring compliance, and discuss the future of cGMP in food packaging for strengthening food safety.
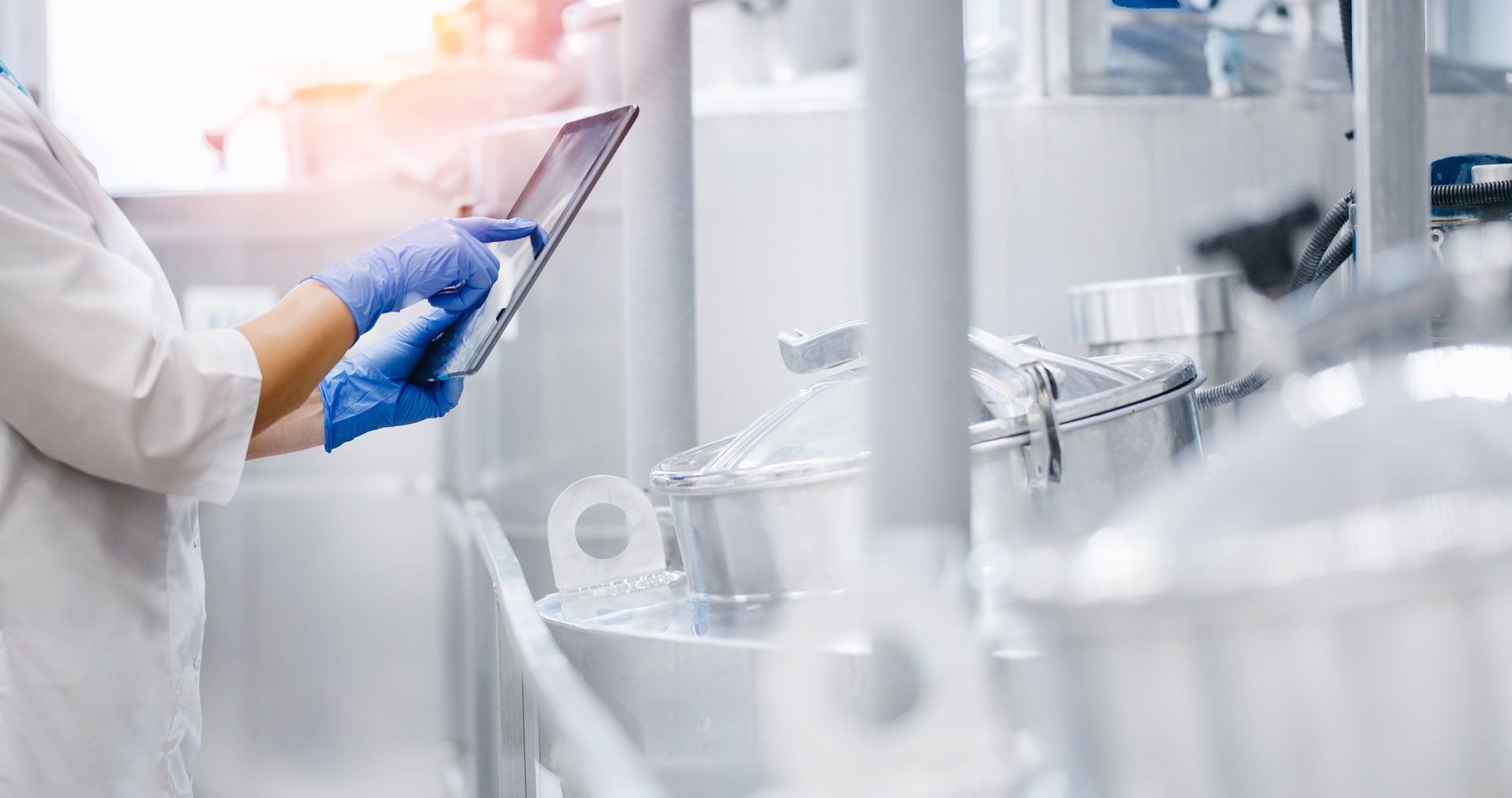
Current Good Manufacturing Practices Food safety is of utmost importance in the food industry, and several systems work together to prevent foodborne illnesses. This article explores the harmonization of Current Good Manufacturing Practices (cGMP), Hazard Analysis and Critical Control Points (HACCP), and Hazard Analysis and Risk-based Preventive Controls (HARPC) in ensuring food line safety. We will delve into the synergy between these systems, the role of critical control points, and their practical application in both automatic and manual counting devices. Additionally, we will discuss how cGMP, HACCP, and HARPC optimize automatic filling machines for enhanced food safety. This is the second in a series of articles on cGMP. Read the others here: Harnessing the Power of cGMP in Preventing Foodborne Illness: A Deep Dive into Food Line Safety Measures Delving into cGMP: Its Crucial Role in Food Packaging and Safety Decoding HARPC: Its Role in Foodborne Illness Prevention and the Importance of Critical Control Points
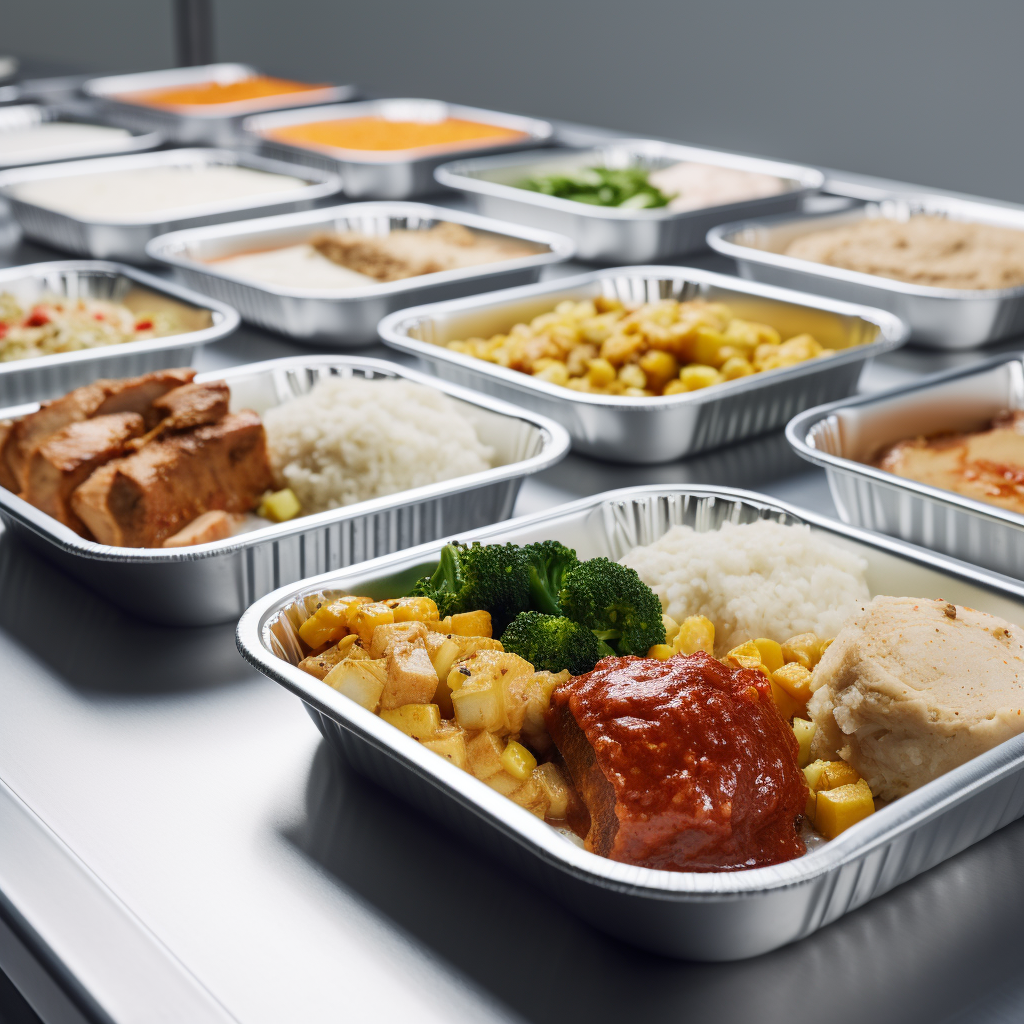
In this article, we explore the crucial role of Current Good Manufacturing Practices (cGMP) in ensuring food safety and preventing foodborne illnesses. We'll delve into the significance of hazard analysis and critical control points (HACCP) and how they contribute to mitigating risks. Additionally, we'll discuss the role of Hazard Analysis and Risk-based Preventative Controls (HARPC) in enhancing food safety measures. This is the first in a series of articles on Good Manufacturing Processes in Food Processing. In this article: Understanding the Importance of cGMP in Food Packaging How Hazard Analysis and Critical Control Points (HACCP) Prevent Foodborne Illness The Role of Hazard Analysis and Risk-based Preventative Controls (HARPC) in Food Safety Critical Control Points in Food Packaging The Intersection of cGMP, HACCP, and HARPC in Food Safety