Automated Filling Machines and Your Business
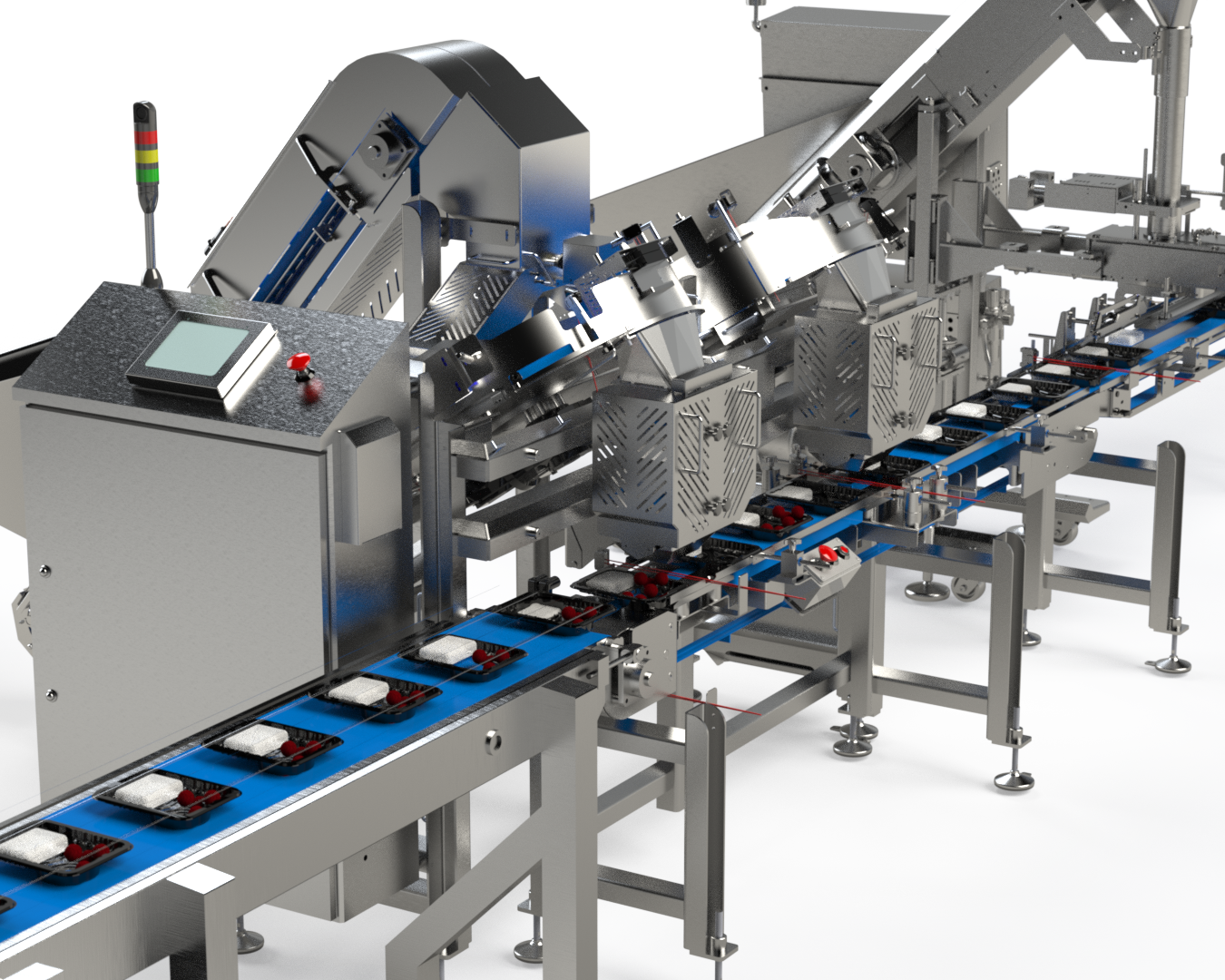
In today’s fast-paced food industry, where efficiency, precision, and quality are paramount, the role of automated filling machines has never been more critical. These technological marvels have transformed the way food products are packaged, offering manufacturers unprecedented control over speed, accuracy, and hygiene. Whether it’s filling a bag of rice, a bottle of sauce, or a ready-made meal container, automated systems ensure consistent results while reducing labor costs and product waste.
This revolution in food packaging is driven by the need to meet increasing consumer demand for convenience and sustainability without compromising quality. With advanced features like IoT integration, volumetric precision, and high-speed operation, automated filling machines cater to a wide range of applications, from beverages to dry goods.
In this article, we’ll explore the types of automated filling machines available and how they work, delve into their numerous benefits, and discuss key considerations for choosing the right solution. We’ll also highlight modern trends like sustainability and smart technology, and share real-world success stories of businesses that have embraced automation to stay competitive. By the end, you’ll understand why investing in an automated filling machine is essential for any food processing company aiming for growth and efficiency.
Key Takeaways
- Automated filling machines revolutionize food packaging by enhancing production speed, accuracy, and hygiene while reducing labor costs and product waste.
- Different types of filling machines cater to various product needs, including volumetric fillers for precise portioning, liquid fillers for beverages and sauces, and powder fillers for dry goods.
- Key benefits of automation include improved efficiency, consistency, and scalability, making these machines essential for companies aiming to meet growing consumer demands.
- Modern advancements like IoT integration and sustainability features make automated filling machines smarter, more efficient, and aligned with eco-friendly practices.
- Choosing the right machine involves considering product type, production volume, and container size, as well as long-term scalability and cost-effectiveness.
Types of Automated Filling Machines
Volumetric Fillers: The Precision Experts
Volumetric filling machines are ideal for products that require precise portioning, such as cooked rice, pasta, or granular dry goods. These machines measure exact volumes, ensuring consistency across every package. For example, if you’re packaging ready-made meals, volumetric fillers can precisely deposit pre-measured portions, maintaining both quality and consumer trust.
Unique insight: Many manufacturers overlook the importance of fill consistency for customer satisfaction. However, a slight variation in product portions can lead to dissatisfied customers and lost revenue. Investing in a high-precision volumetric filler ensures brand reputation remains intact.
New Paragraph
Liquid Filling Machines: For Beverages and Sauces
Liquid filling machines come in multiple configurations, including overflow fillers, piston fillers, and pump fillers, each designed for specific applications. For instance, overflow fillers are excellent for clear liquids, ensuring every bottle is filled to the same visual level. On the other hand, piston fillers handle viscous products like salad dressings and mayonnaise with ease.
Key Benefit: Liquid fillers are particularly suited to the beverage industry, where speed and hygiene are critical. Modern advancements like integrated CIP (clean-in-place) systems ensure reduced cleaning time and sanitary operations.
Benefits of Automated Filling Machines
Enhanced Efficiency
Automated filling machines can process thousands of containers per hour, significantly increasing production speed and reducing downtime. This is especially valuable for high-volume operations.
Improved Accuracy
By delivering consistent fill levels, automated systems reduce waste and ensure every package meets quality standards. This level of precision builds consumer trust and minimizes production costs.
Hygiene and Safety
The food industry demands strict hygiene. Automated systems reduce manual handling, thereby minimizing contamination risks and ensuring compliance with safety regulations.
Cost Savings
Although the initial investment in an automated filling machine can be significant, the long-term savings on labor and waste make it a cost-effective solution.
Choosing the Right Automated Filling Machine
Factors to Consider
· Product Type: Different machines are suited to liquids, solids, or powders.
· Production Volume: High-speed volumetric fillers are ideal for large-scale operations.
· Container Size: Machines with adjustable settings provide flexibility.
Customization and Scalability
Investing in a machine that can grow with your business ensures long-term ROI and adaptability to future production demands.
Modern Trends in Filling Machine Technology
Sustainability
Eco-conscious businesses are turning to automated systems compatible with biodegradable or recyclable packaging materials. Some machines also feature energy-efficient designs.
Smart Manufacturing
IoT integration allows for predictive maintenance and real-time monitoring, reducing downtime and improving operational efficiency.
FAQs on Automated Filling Machines
1. What are the main types of automated filling machines?
Automated filling machines include volumetric fillers for precise portioning, liquid fillers for beverages and sauces, and powder fillers for dry goods like spices. Each type is designed for specific applications to ensure accuracy and efficiency in food packaging.
2. How do automated filling machines improve efficiency in food processing?
Automated filling machines enhance efficiency by reducing labor requirements, minimizing product waste, and ensuring consistent fill levels. High-speed volumetric fillers, for example, can process thousands of containers per hour, streamlining production.
3. What factors should I consider when choosing an automated filling machine?
Consider your product type (liquid, powder, or solid), production volume, container size, and desired scalability. For instance, high-speed volumetric fillers are ideal for large-scale operations, while liquid fillers may be better for beverages and sauces.
4. Are automated filling machines suitable for eco-friendly packaging?
Yes, many modern machines are compatible with sustainable packaging materials, such as biodegradable or recyclable containers. Some also feature advanced technologies to reduce energy consumption, aligning with eco-conscious production goals.
5. What maintenance is required for automated filling machines?
Regular maintenance includes cleaning, checking for wear on parts, and ensuring calibration accuracy. Many machines now include IoT integration for predictive maintenance, helping to avoid costly downtime and repairs.
Automated filling machines have become indispensable in the food processing industry, offering unparalleled advantages in speed, precision, and efficiency. From volumetric fillers for precise portioning to liquid and powder filling machines tailored for specific products, these systems address the diverse needs of modern food manufacturers. By automating the packaging process, businesses can reduce labor costs, minimize product waste, and ensure consistent quality—key factors for staying competitive in a demanding market.
If you’re ready to revolutionize your food packaging process, now is the time to explore the latest in automated filling technology. Visit Multi-Fill.com to learn more about how advanced filling machines can transform your production line and elevate your business to the next level.
References
- Multi-Fill. “Everything You Need to Know About a Filling Machine”.
- Multi-Fill. “Why Should You Automate Your Filling Systems?”.
- FMI Blog. “Automatic Filling Machine Market Analysis”.
- Food Mag. “Introducing ESKO Australia and Alfa Machine’s Recyclable Technology”.
- Healthcare Packaging. “Automatic Assembly and Vial-Filling Machine”.
Designing a food filling line: Product is king

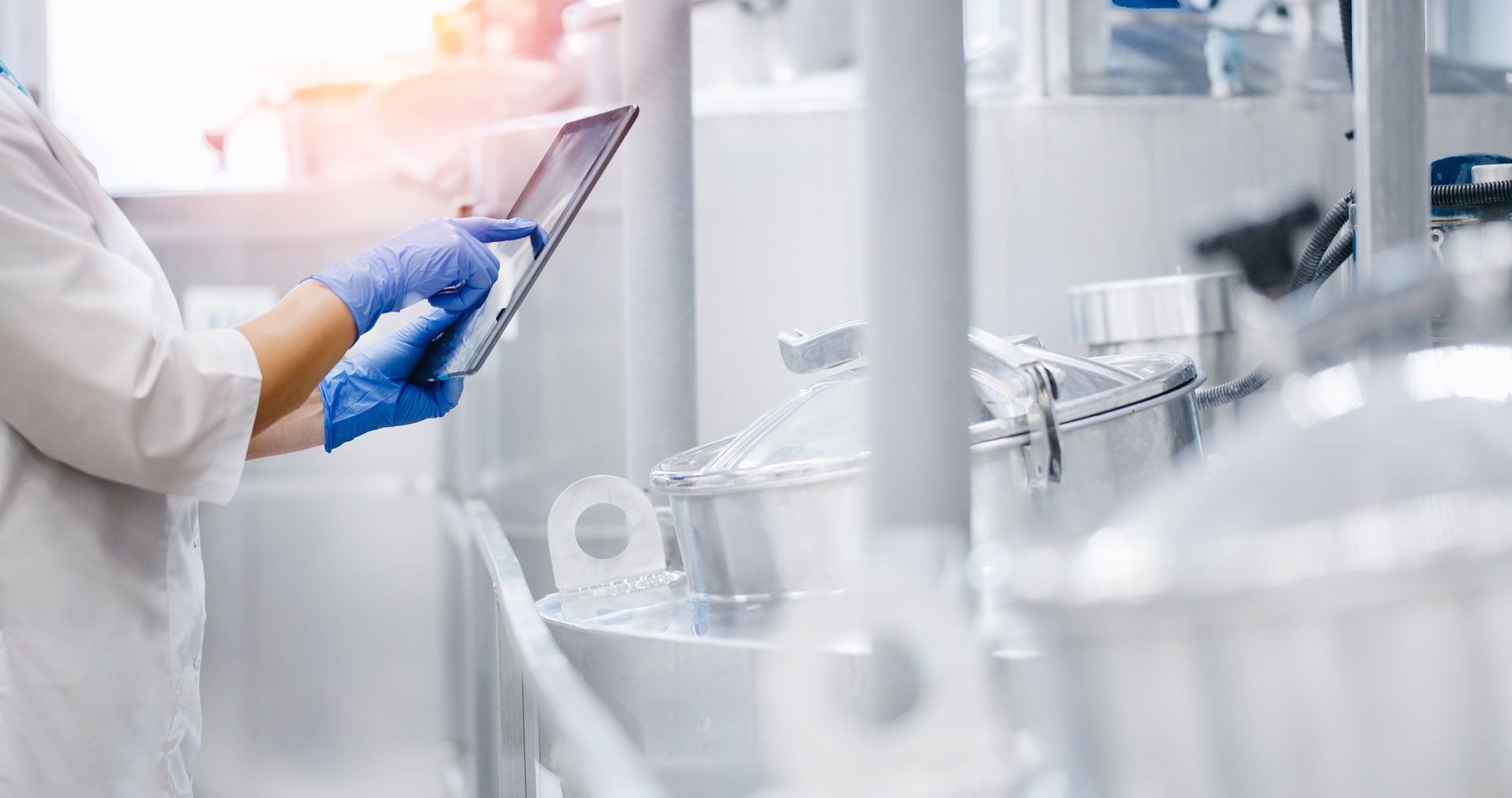
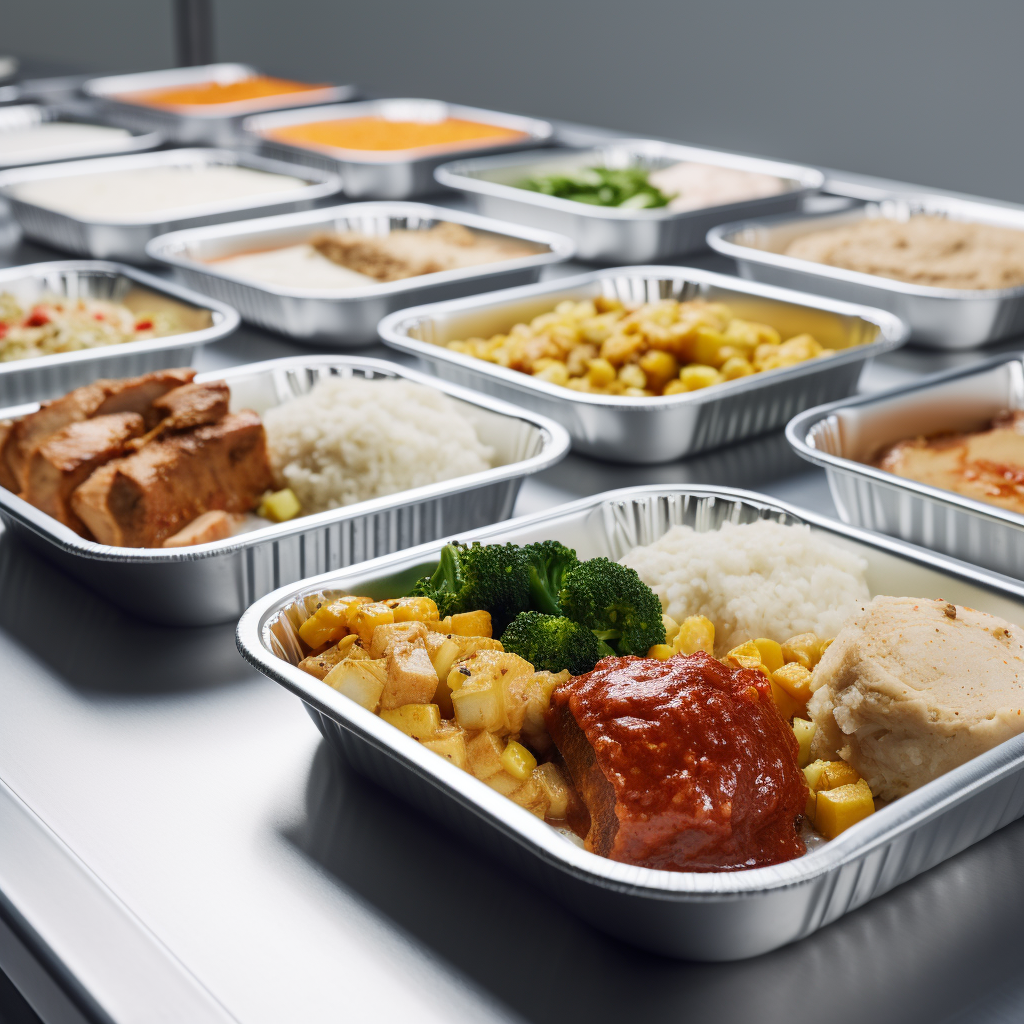