Michael Naylor • January 26, 2020
Are Volumetric Fillers Better Suited to Your Business?
Learn how they work and what makes them unique
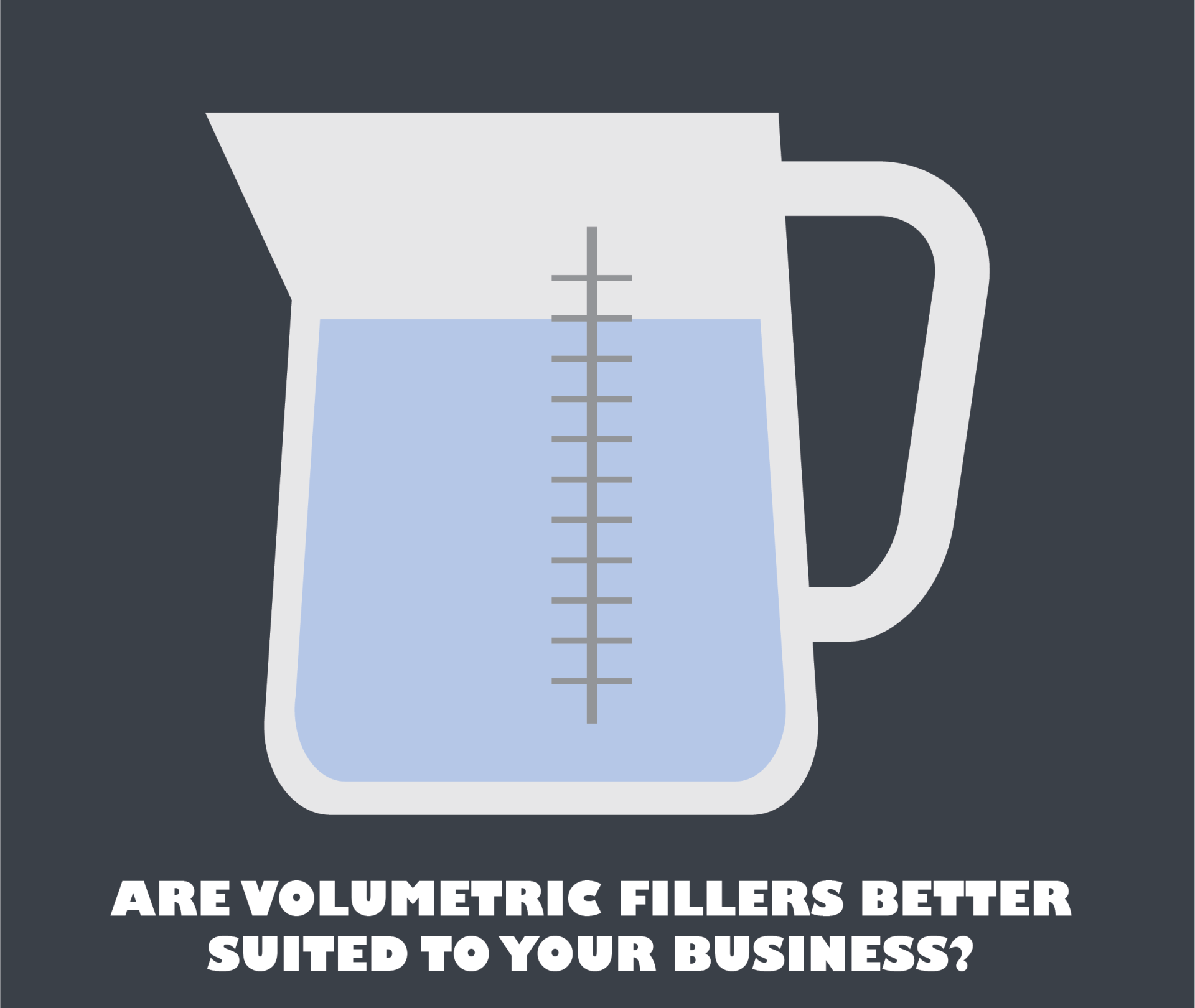
In the processed food industry, selecting reliable filling equipment is about looking for precision, speed and accuracy. Whether you are exploring your first automated filling machine, or you are a seasoned player with sophisticated systems, you always want ‘faster’ or ‘more efficient’ filling solutions.
This is where the volumetric fillers from Multi-Fill come in. However, since every filling system works on unique technology, you will first need to know which one is better suited to your operations. Learn more about the differences in filling solutions, and how our volumetric fillers could transform the cost, efficiency and quality of your filling and packaging processes.
How to Shortlist a Filling System
The food packaging market is flooded with a number of filling systems that work on different technologies. Deciding which solution works best for your business requires you to:
1. Know the basic technologies behind various types of filling machines. From flow filling and volume filling, to counting filling,volumetric piston/pump filling to weighing scale machines, each system works on its own logic of batching, portioning, and dropping the material into the packaging.
2. Review the features of the type of system you select. This includes customization and upgrade capabilities, temperature requirements, anti-corrosion properties, ease of sanitation, and compliance with applicable norms.
3. Check the compatibility of the filling solution with the rest of your production line, including processing, packaging and sealing machines.
4. Evaluate whether the machine’s pricing fits within your planned budget. But is the cheapest machine upfront the less costly overall?
How Do Volumetric Fillers Work?
Here is how volumetric fillers work:
• It measures a volume to get to a weight based on the density of the product.
• Product density is an important factor when filling volumetrically. Actual weights in the containers will vary depending on variation in product densities, which is influenced by the size and shape of the particulates, temperature, recipe, processes used by a customer, etc.
• As it is based on product density, maintaining stable densities during the filling process is critical to good accuracy over a production run.
Other factors affecting the accuracy of a product are: mix/homogeneity, temperature, piece size, production process (batch vs. Continuous operation, downtime, consistency of feeding of the filler).
What makes volumetric fillers so unique is their ability to:
• Drop a specific volume of product into the desired packaging. For example, if you are into packing airline meals, you may want a precise volume of food to be filled into each compartment of the tray.
• Create pure volume efficiencies, instead of weight or level. For example, two bottles filled by the same volumetric filler may show inconsistent levels visually, but the volume of the product will be precise and identical in both.
• Handle difficult-to-fill products: These fillers offer clean and accurate portioning for items, such as cooked rice, cooked pasta, cereal, refrigerated salads, etc., which are usually tough to fill automatically without creating wastage or spills.
Best-In-Class Volumetric Filling Solutions by Multi-Fill
At Multi-Fill, we specialize in advanced volumetric filling solutions for difficult-to-fill products. Depending on the model you select, our range of volumetric fillers
can:
Handle filling from anywhere between 5 to 120 containers per minute.
Cater to lower speed production lines in R&D labs and pilot plant operations, as well as high speed lines for stickier products, or large volume packaging.
Take advantage of our compact designs, customization flexibility, and ease of integration. Our filling and distribution solutions are compatible with all types of container conveying systems, including continuous and intermittent motion, single or multi-lane, and horizontal or vertical bagging machines.
For high quality, high speed volumetric filling solutions at competitive prices, rely on a recognized industry leader. Call Multi-Fill at 801-280-1570 to know more about our products or contact us online.
Designing a food filling line: Product is king

Food packaging plays a vital role in ensuring the safety and quality of the food we consume. To maintain high standards and prevent foodborne illnesses, the food packaging industry follows a set of regulations known as Current Good Manufacturing Practices (cGMP). In this article, we will delve into cGMP and explore its impact on preventing foodborne illness. We will also take an inside look at how cGMP is implemented on a food factory line, the role of food filling equipment in ensuring compliance, and discuss the future of cGMP in food packaging for strengthening food safety.
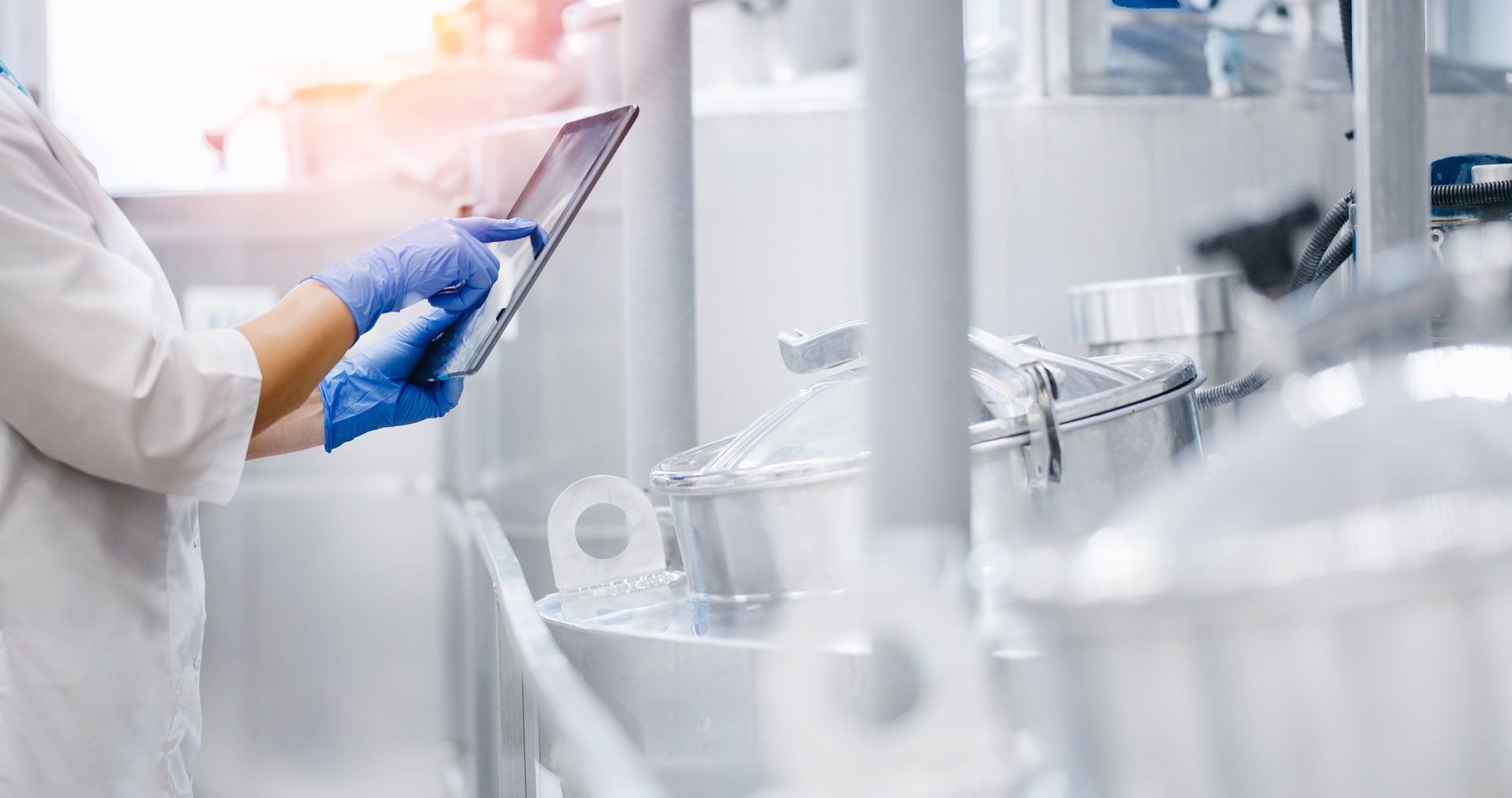
Current Good Manufacturing Practices Food safety is of utmost importance in the food industry, and several systems work together to prevent foodborne illnesses. This article explores the harmonization of Current Good Manufacturing Practices (cGMP), Hazard Analysis and Critical Control Points (HACCP), and Hazard Analysis and Risk-based Preventive Controls (HARPC) in ensuring food line safety. We will delve into the synergy between these systems, the role of critical control points, and their practical application in both automatic and manual counting devices. Additionally, we will discuss how cGMP, HACCP, and HARPC optimize automatic filling machines for enhanced food safety. This is the second in a series of articles on cGMP. Read the others here: Harnessing the Power of cGMP in Preventing Foodborne Illness: A Deep Dive into Food Line Safety Measures Delving into cGMP: Its Crucial Role in Food Packaging and Safety Decoding HARPC: Its Role in Foodborne Illness Prevention and the Importance of Critical Control Points
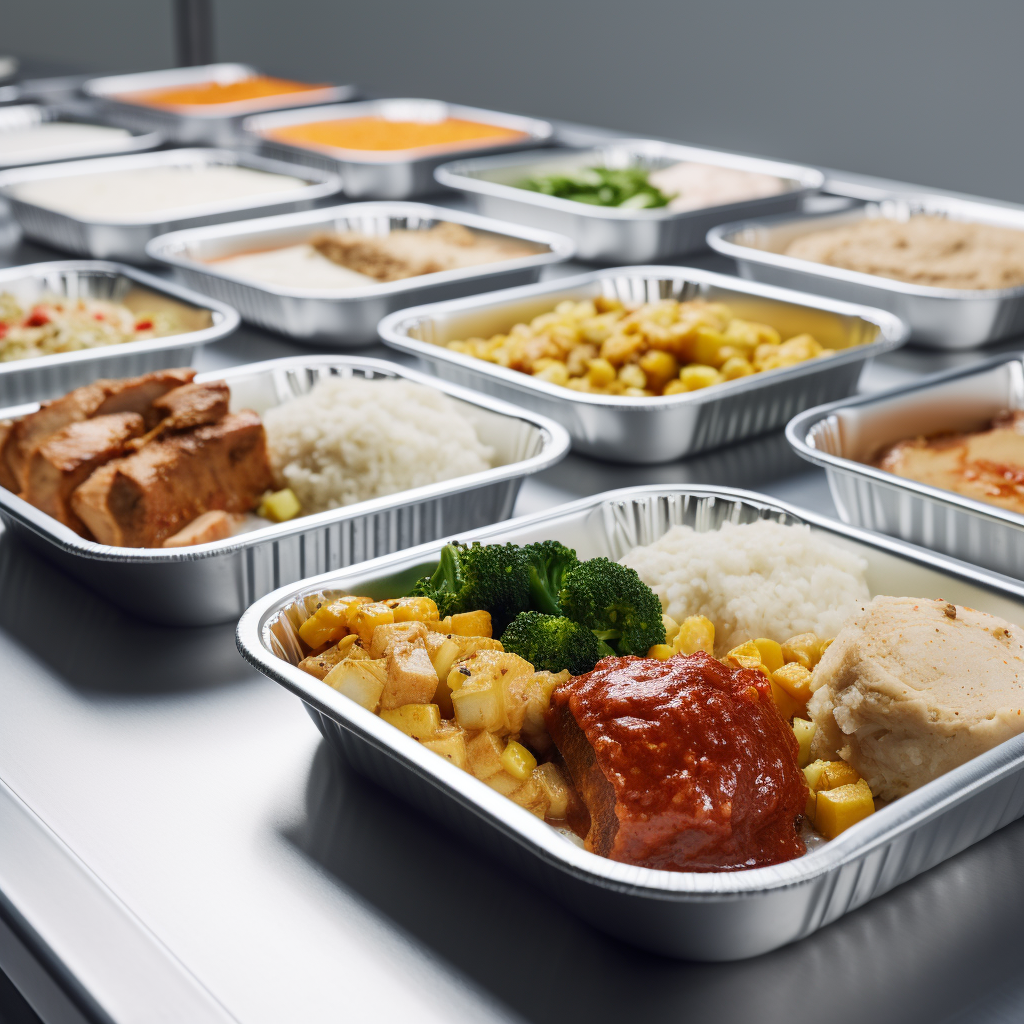
In this article, we explore the crucial role of Current Good Manufacturing Practices (cGMP) in ensuring food safety and preventing foodborne illnesses. We'll delve into the significance of hazard analysis and critical control points (HACCP) and how they contribute to mitigating risks. Additionally, we'll discuss the role of Hazard Analysis and Risk-based Preventative Controls (HARPC) in enhancing food safety measures. This is the first in a series of articles on Good Manufacturing Processes in Food Processing. In this article: Understanding the Importance of cGMP in Food Packaging How Hazard Analysis and Critical Control Points (HACCP) Prevent Foodborne Illness The Role of Hazard Analysis and Risk-based Preventative Controls (HARPC) in Food Safety Critical Control Points in Food Packaging The Intersection of cGMP, HACCP, and HARPC in Food Safety