Volumetric fillers and ready meal packaging solutions
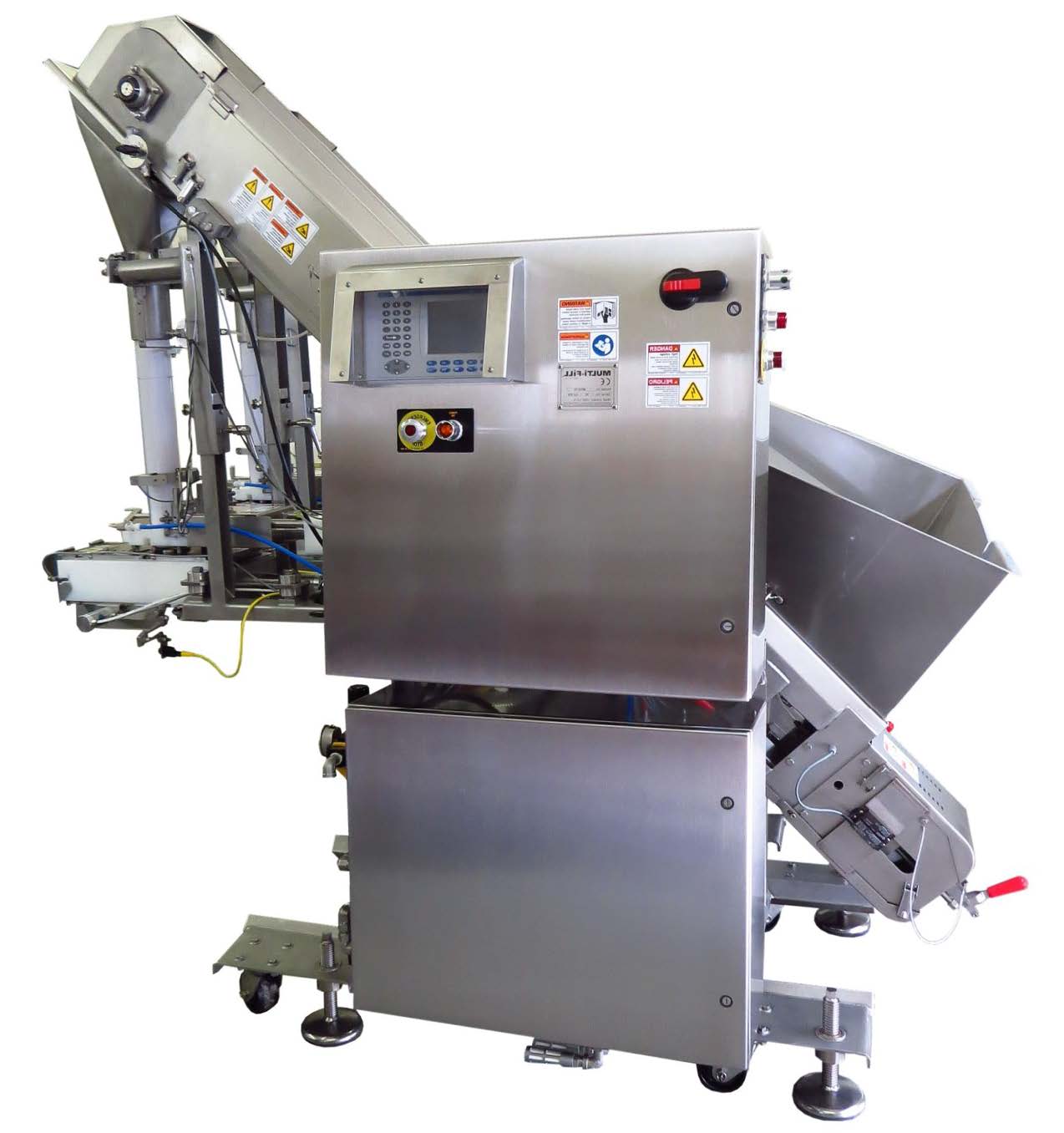
Volumetric fillers are a vital part of the rapidly growing ready meal industry. In 2019,this industry was valued at $159.5 billion globally and expected to expand by 5% each year. Together with the demand for ready-to-eat meals, consumers also expect fresh, additive-free foods that are healthy and have a relatively long shelf life.
There is rising demand to fill the variety of quality foods that consumers want, with accuracy, versatility, speed, precision, and easy cleaning. Multi-Fill specializes in designing and supplying volumetric filling machines and other ready meal packaging solutions that fulfill all these criteria. In this article, we will tell you everything you need to know about the fillers that feed this industry and its growth.
Commonly asked questions about filling machines
When the makers of ready meal products start shopping around for volumetric fillers, they usually ask a series of similar questions. Here are the most commonly asked ones, along with their definitive answers.
What is a filling machine?
A filling machine is a piece of equipment that is designed to fill measured quantities of foods (or beverages and other liquids - although we do not build machines for this purpose) for distribution to retail stores, canteens, and similar facilities. Filling machines can range from hand-operated to fully automated.
What is a volumetric filling machine?
Volumetric filling machines are equipment designed to dispense precise, measured quantities of a product into the required packaging. They work according to the volume of product to be delivered, or by achieving the correct weight by dosing the proper volume of product based on its density. Volumetric fillers are configurable, meaning they can be set to deliver varying quantities of product as needed.
How does a liquid filling machine work?
Whereas volumetric filling machines work by dispensing a specified volume of solid or liquid products, liquid level filling machines operate by filling a container up to a particular level. Volumetric fillers will always deliver the same programmed quantity, regardless of whether there is a fill-line on the container. On the other hand, liquid-level fillers always fill up to a specific level, even if the weight or volume of the product in each container differs.
How does a volumetric filler work for particulate products?
A volumetric filler measures out a specified volume of particulate (or mostly solid) product to get to a required weight, based on the density of the product. Density is an important factor in volumetric dispensing. Weights will vary depending on the density of the product. Since most foods are sold according to weight, the configuration of volumetric machines depends on finding the right volume of food to reach the required mass. Maintaining stable densities during the filling process is critical to good accuracy over a production run.
What is gravimetric filling?
As explained above, volumetric fillers work by measuring out a particular volume of a product. On the other hand, gravimetric filling machines dispense an accurately measured amount of the products according to weight.
What is auger filler?
An auger filler works by filling material into a container with a screw-like mechanism called an auger, which delivers specific doses of the product as it rotates. Auger fillers are mostly used for liquids and free-flowing powders, rather than solid foods.
What is an aseptic filling machine?
Aseptic filling machines are used for sterile processing, a product packaging process used in the pharmaceutical industry, and for the dispensing of some foods. In this process, the product, the packaging and the machines need to be absolutely sterile. The machines are designed to be easily cleaned and sterilized.
What is FFS packaging?
Form-fill seal (FFS) technology allows for the forming, filling and sealing of a distribution-ready package in a single step. Other filling methods generally perform sealing and filling in separate steps. This method involves thermoformable plastic and could take place on either vertical or horizontal bagging and sealing machines.
Vegan Protein (imitation meat) filling machines
The read-made meal industry needs to cater to a wide range of tastes and preferences. Difficult-to-dispense products like couscous and quinoa are increasingly popular, as are vegan protein products like plant-based, imitation hamburger, sausages, etc. Such products require specialized filling equipment.
We manufacture filling machines and equipment for various products
Multi-Fill has developed several machines that are specially designed to dispense products that are notoriously difficult to fill. The most important factors in these machines are easy cleaning and anti-clumping functions, which allow these products to flow freely and dispense consistently into every package.
Why volumetric technologies for your product line?
Volumetric technologies ensure accuracy, speed and precision on your production line. Each of your packages will be consistently and correctly filled, and your filling line will flow smoothly without the risk of stoppages due to product build-up in the fill nozzles or hoppers. You will be able to guarantee the quality and consistency of your products while speeding up your output.
Our innovative filling machine systems
Multi-Fill supplies several innovative filling systems to the ready-meal industry. They include the following:
- The MPFMP-060 is a volumetric filler ideally suited for lower speed production lines, research and development labs, and pilot plant operations. The product is loaded on to the top pan and manually fed into the dosing head by an operator.
- The MPFSH-75 fills 60 to 75 containers per minute. It can be upgraded at a later date to a MPFSC-120 for increased speed and/or different products. The MPFSH-075 is recommended for applications where more automatic product feeding is required. It is suitable for lower speeds, easier (looser) products, smaller fill weights.
- The MPFSC-120 is our high-speed machine, which fills up to 120 containers per minute for most products. It is recommended where not only more automatic feeding of the product is required but the capability of higher speeds, stickier products or larger volumes are needed.
Top-quality volumetric fillers for a variety of industries
The three Multi-Fill volumetric filler models can be used to dispense an astonishing array of food products. Whether your company supplies a wide-ranging menu of ready-made meals or focuses on one or two specific products, one of our machines will likely offer you the solution you need. The products that can be dispensed with our machines include the following:
- Vegetables
- Pasta
- Rice
- Wholegrains
- Cereals
- Pet Foods
- Candy and desserts
- Meats
- Fruit
- Prepared salads
- Ready-made meals including combinations of several ingredients, such as rice, meat and vegetables, for example.
Get a reliable filling machine for your product line
To find a reliable filling machine that is perfect for your product line, consult with Multi-Fill. Once we know what product(s) you are looking to fill, we will be able to recommend the right machine for you, and help customize it to perfect your filling and packing processes.
Customizable volumetric dosing machines
Although Multi-Fill supplies three standard volumetric dosing machines, we can also configure, upgrade, or customize these to work with your particular product and process. We can attach batch-feeding hoppers to your MPFSH-075 or MPFSC-120, for example, or we can design a special patented distribution solution that works with your existing layout.
Patented technology to fill bottles, jars, trays, bags, or plastic containers
We can take our solutions and integrate them into your existing specific line layout, including multi-lane conveying systems or vertical pouch machines. Custom-designed distribution systems can be used in combination with our volumetric fillers or other portioning systems such as vibrator feeders, multi-head scales, rotary pocket fillers, or counting machines.
The distribution systems can be used in combination with our volumetric fillers or other portioning systems such as vibrator feeders, multi-head scales, rotary pocket fillers, or counting machines.
Major components of a filling machine
Although the design of filling machines can differ extensively in their specifics, they generally consist of the following essential components:
#1 Hopper
A hopper is a funnel-like object into which product is fed for delivery into packages via the filling head or nozzle below.
#2 Filling head/nozzle
The filling head or nozzle is the part which dispenses the dose of product from the filler into the container.
#3 Mechanical drive System
The mechanical drive system is the expertly engineered mechanism that operates the machine in a carefully automated, perpetual series of metered doses of products. It is programmed to ensure that the dispensed doses are synchronized with the movement of the containers.
#4 Sensors and signals
Sensors and signals are essential to the correct automation of our filling systems. At any given moment, our sensors synchronize products and containers by checking if there is a container to fill, and if there’s product in the chute to dispense into the container. Signals are sent and received between all the machines on the line to start, end or resume filling. Together the sensors and signals ensure that the filling process runs continuously, accurately and without waste.
#5 PLC control system
Programmable logic controllers (PLCs) are the mini-computers built into our systems, which enable the control and automation of the production line. The PLC can control the speed of the process and the volume of product to be dispensed, among other functions. The PLC is programmed, monitored and adjusted through the human-machine interface (HMI).
#6 HMI control system
The human-machine interface (HMI), is the touch screen or button-operated system, where the operator controls the machine and monitors its functions.
Advantages of our filling machines
There are many volumetric filling machines on the market. Aside from the high fidelity and accuracy of our solutions, here are three key reasons why you should choose Multi-Fill’s custom-designed machines.
#1 Corrosion-resistant stainless steel (food grade)
Each one of our machines is made of food-grade, corrosion-resistant stainless steel. They are built to last and to maintain the highest standards of health and hygiene. They are extremely easy to clean and allow for fast product changeovers.
#2 Programmable to fit your product line
No matter what food you want to dispense and what quantities, our machines will do the job for you. What’s more, if you want to change to a different product in different quantities, you can easily do so by cleaning the hopper and fill head and entering new parameters into the PLC.
#3 Built in the USA
Multi-Fill’s products are proudly designed and built right here in the United States. We have been supplying and servicing filling equipment for decades. In fact, several of our clients are still successfully running machines we first supplied to them in the 1980s!
For reliable, high-quality volumetric fillers for your read-made meal product line,
contact Multi-Fill.
Designing a food filling line: Product is king

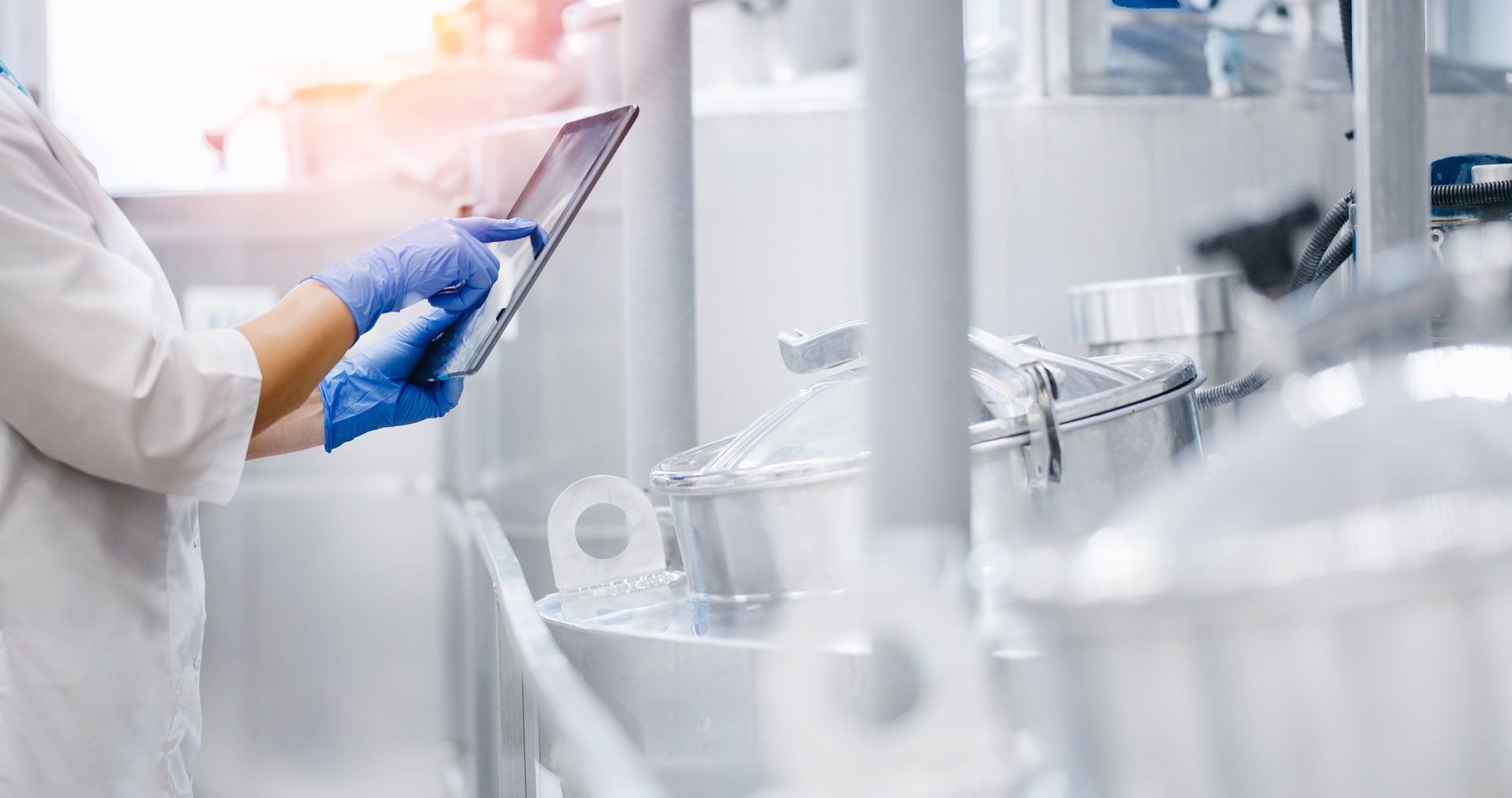
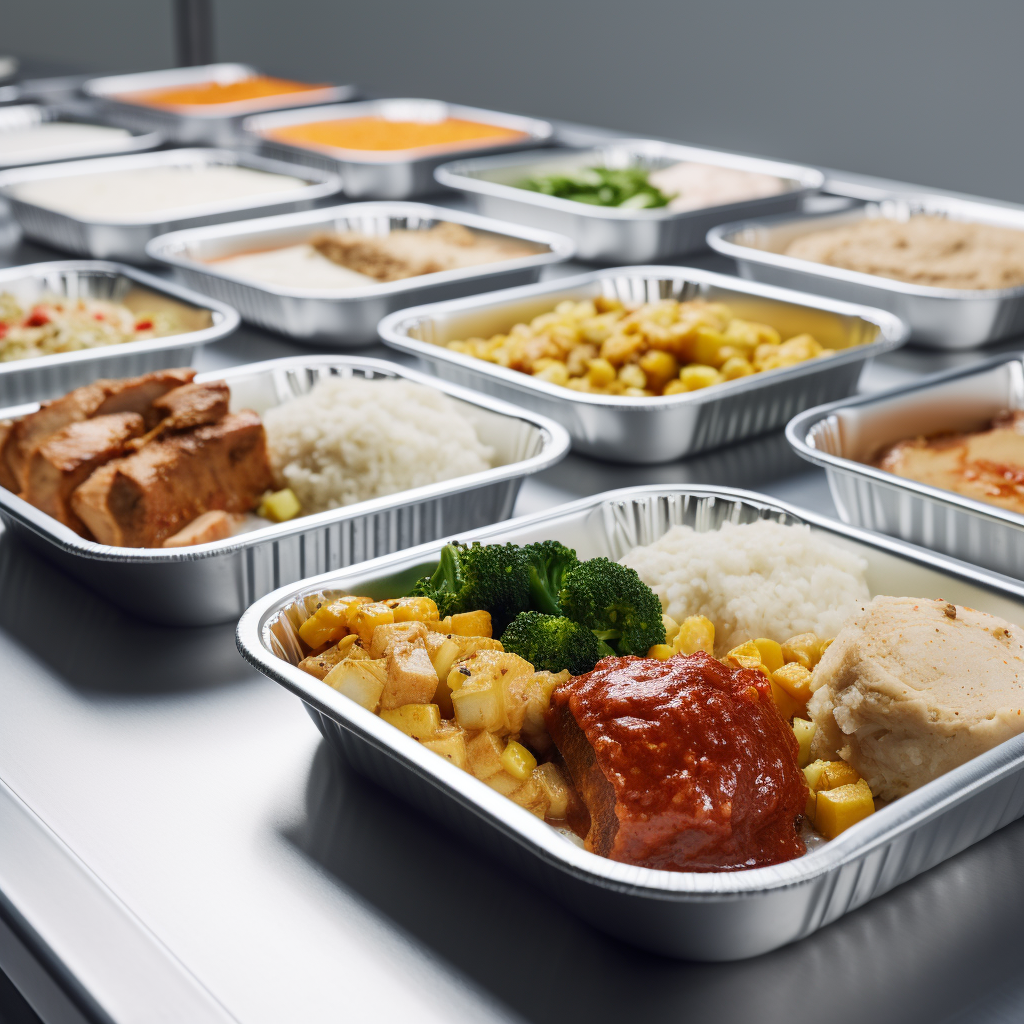