How to Improve Your Filling Machine Accuracy
Improving filling machine accuracy can help businesses reduce waste, increase efficiency, and improve product quality. However, achieving high levels of accuracy can be challenging, especially when dealing with complex fluids, variable container shapes, and production line speed changes. Fortunately, there are several strategies that businesses can use to improve filling machine accuracy, including optimizing equipment design, using advanced sensors and controls, and implementing regular maintenance and calibration procedures.
In this blog post, we’ll cover five ways you can improve the accuracy of your packaging operations.
Train Your Team Properly: Prevention is Better Than the Cure
By investing in comprehensive training programs, you can ensure that your operators understand how to operate the equipment correctly and efficiently. This includes training on best practices for handling complex fluids, maintaining proper line speeds, and managing variable container shapes. Additionally, training can help operators recognize common errors and malfunctions, enabling them to troubleshoot and resolve issues before they impact production. Ultimately, prevention is better than a cure, and a well-trained team can help minimize downtime, reduce waste, and improve product quality.
Choose the Filling Machine Wisely
Choosing the right machine is critical for achieving high levels of accuracy in your filling process. When selecting a filling machine, it's essential to consider factors such as the viscosity of the fluid, the shape and size of the container, and the desired fill level. Investing in a machine that is designed specifically for your application can help minimize errors and improve efficiency. Additionally, choosing a machine that features advanced sensors and controls can enable you to monitor and adjust fill levels in real time, further increasing accuracy and consistency. By selecting a
filling machine wisely, businesses can achieve optimal performance and maximize their return on investment.
Let the Manufacturer Know of Any Issues
Manufacturers rely on customer feedback to continually improve their products. So, addressing any issues you encounter can help them identify and correct potential design or manufacturing flaws. Additionally, by working closely with the manufacturer, you may be able to obtain technical support, including remote troubleshooting, onsite service, or replacement parts. These services can help ensure your filling machine operates properly, reducing errors and improving the level of accuracy. By communicating with the manufacturer and seeking their support, businesses can maximize the potential of their filling machine and minimize downtime.
Get a Professional to Take a Look
Professionals can provide a fresh perspective on your production process and identify potential sources of error or inefficiency. They may also be able to recommend adjustments or upgrades to your equipment or processes that can help improve accuracy, reduce waste, and increase throughput. Additionally, professionals can provide specialized services such as equipment calibration, preventive maintenance, and troubleshooting. By leveraging the expertise of professionals, businesses can ensure that their machines operate at peak performance, enabling them to achieve optimal filling accuracy and efficiency.
Consider Upgrading
Upgrading your filling machine can improve accuracy by incorporating advanced sensors, controls, and software, enabling real-time monitoring and precise adjustments to optimize filling performance.
Looking to upgrade your filling machine?
Consider Multi-Fill’s automated filling machines!
We offer ideal food filling machines for:
- Rice & Pastas
- Salads
- Vegetables and Fruits
- Meats
- And more!
Contact us today to improve your filling machine accuracy!
Designing a food filling line: Product is king

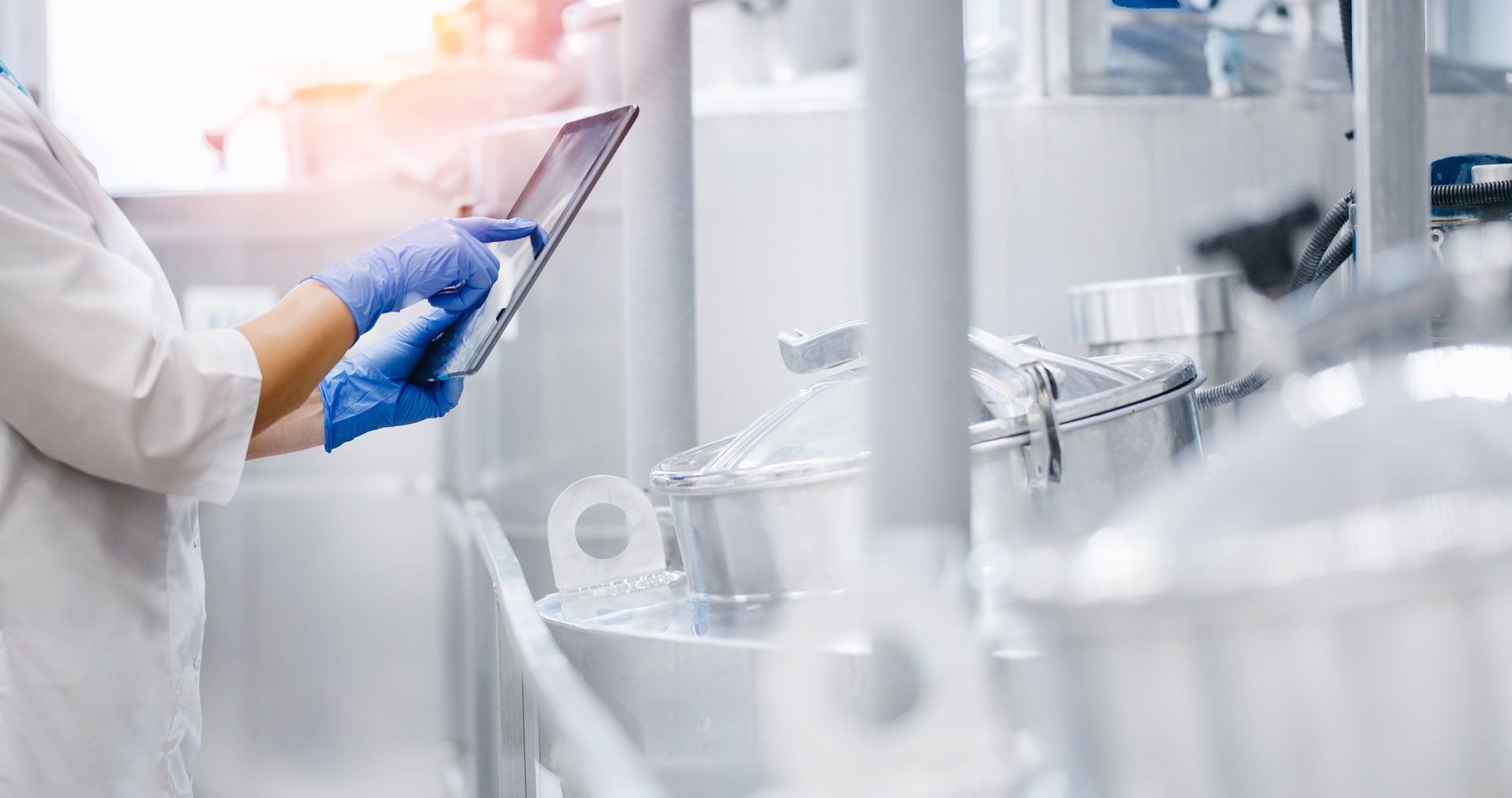
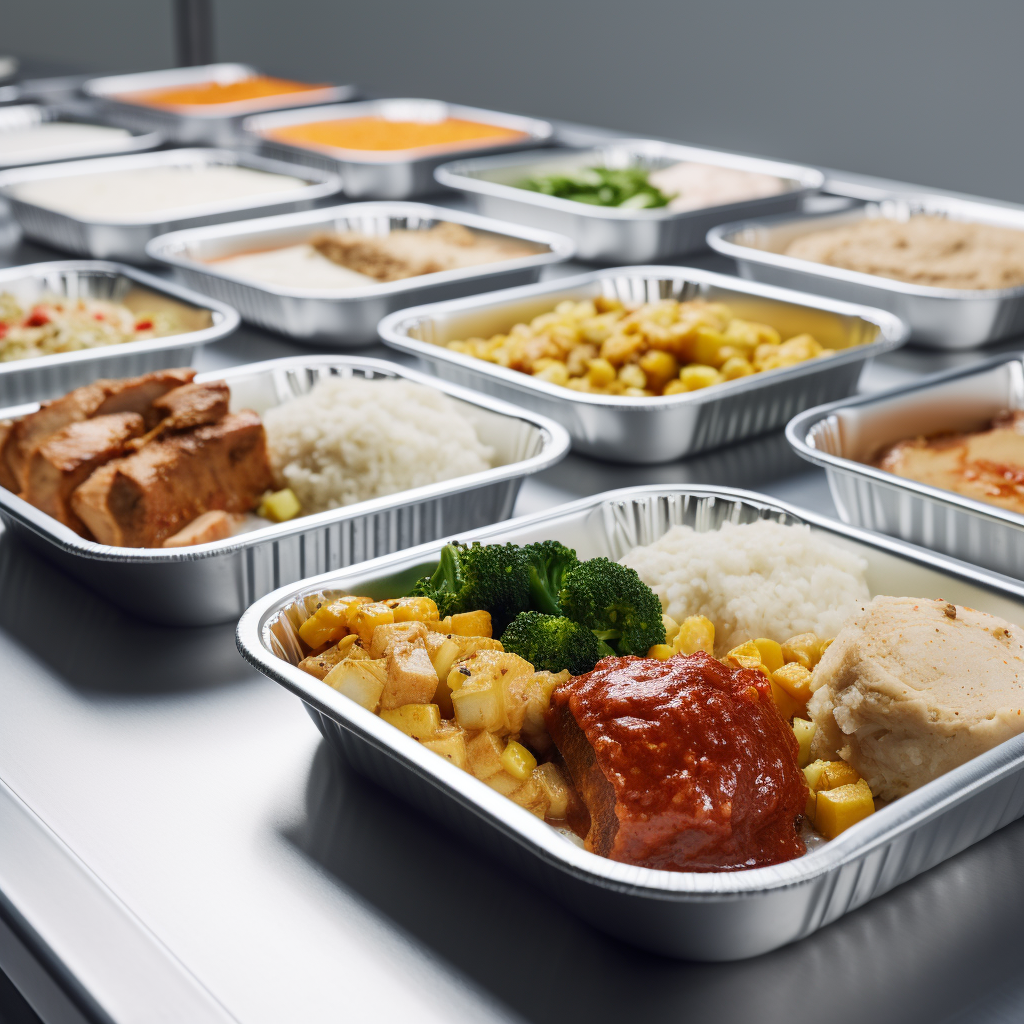